新書推薦:
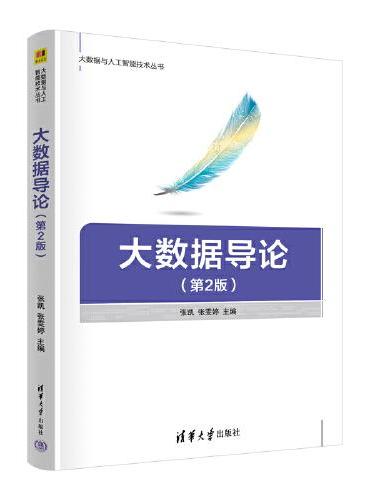
《
大数据导论(第2版)
》
售價:NT$
352.0
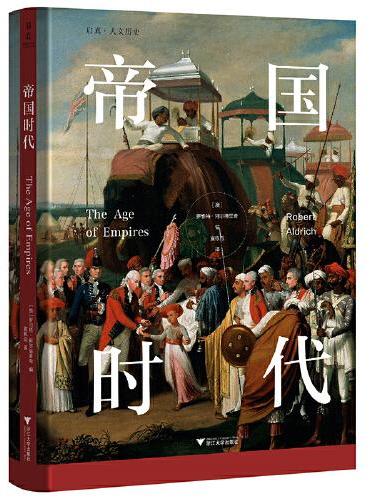
《
帝国时代
》
售價:NT$
959.0
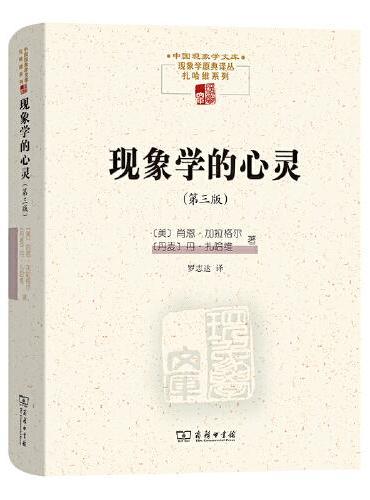
《
现象学的心灵(第三版)(中国现象学文库·现象学原典译丛·扎哈维系列)
》
售價:NT$
500.0
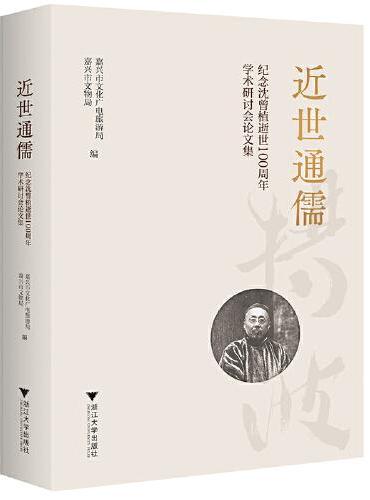
《
近世通儒——纪念沈曾植逝世100周年学术研讨会论文集
》
售價:NT$
857.0
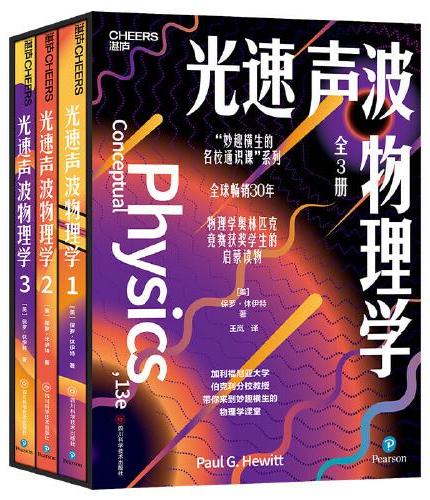
《
光速声波物理学. 1、2、3
》
售價:NT$
2295.0
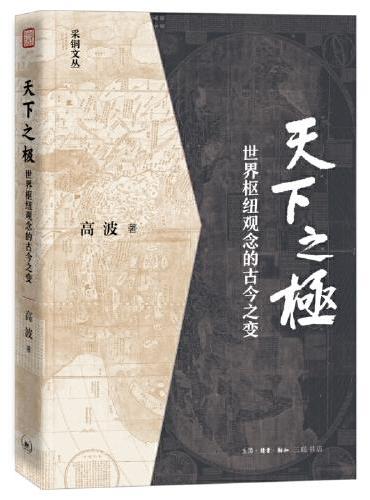
《
天下之极:世界枢纽观念的古今之变
》
售價:NT$
449.0
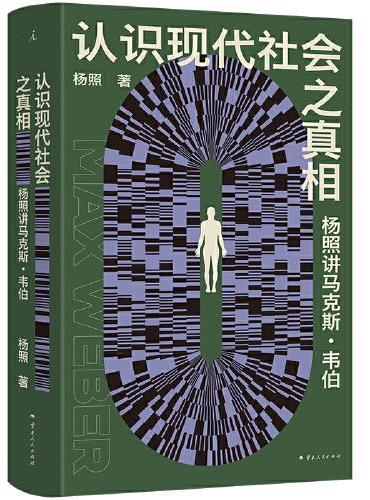
《
认识现代社会之真相:杨照讲马克斯·韦伯
》
售價:NT$
439.0
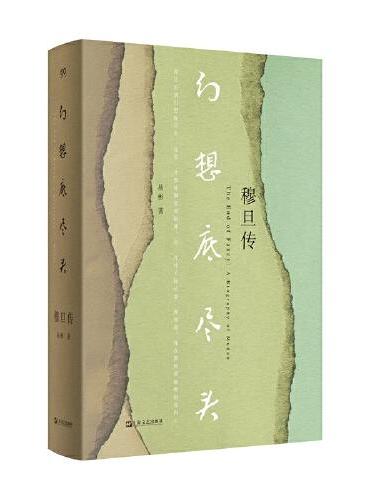
《
幻想底尽头:穆旦传(《穆旦年谱》编撰者历时二十余年心血之作,基于《穆旦评传》精心修订,文献翔实可靠,完整讲述了一位中国诗人与翻译家并不平顺的一生。)
》
售價:NT$
653.0
|
內容簡介: |
这是一本企业推行精益管理的培训普及读本。其目的是能够让基层管理者都知晓精益的价值和精益管理的要求,具备精益管理的素质。
本书主要面向基层管理者,旨在帮助基层管理者了解精益管理的源头、精益管理的原因、推行原则、基本工具和技术等。在整个过程中,基层管理者应了解基层精益管理系统,深刻理解精益管理学知识和实践方法,全面提升精益管理能力。本书具有以下特征:
(1)强系统性。目前市面上关于基层管理者的书籍大多流于从意识、能力的角度告诉人们应该做什么,但却没有专著去集中论述基层精益管理的来龙去脉、起始布局。本书的突出特征是,系统诠释基层精益管理的基本逻辑体系,细化阐述精益管理系统和工作思维模式。
(2)强实用性。本书立足于企业基层工作,以实践性案例为载体,细致地阐述涵盖于内的精益管理理念、知识和工作诀窍,便于基层管理者一边联系实际,一边了解精益管理思想。对于基层管理者而言,本书的实用价值是非常高的。
(3)强逻辑性。本书著述的目的是帮助读者建立基层精益管理的基本逻辑,深刻解析基层精益管理的知识、理念、实践方法,非常便于基层管理者建立起一套精益管理逻辑思维系统。
|
關於作者: |
孙亚彬:制造业企业管理研究与咨询顾问。立正管理咨询有限公司以及华商永续管理咨询有限公司创始人,多家大型制造业企业独立董事。长期服务于中建联、高意光学、中船重工、风帆电池、中国兵器集团的标准化管理建设以及人力资源教育培训工作。著有《IE与单元生产》等国内最早的精益生产管理著作。
易生俊:企业管理研究与咨询顾问。曾任中大咨询公司咨询总监、赛普咨询高级顾问、深圳市梦网科技发展有限公司副总裁、青岛啤酒集团华南营销有限公司管理总监、五洲电路集团总裁助理和武汉市邮政局人力资源部副部长。现为AMT咨询和中大咨询两家咨询公司特聘专家顾问和专家讲师,担任多家公司战略顾问。
专注于流程管理实践16年,从业务流程到管理流程,从生产操作流程到顶层流程设计,均有深入研究。在长期的实践中,不但作为企业管理人员从事流程管理实践活动,而且作为咨询顾问为多家企业实施流程咨询项目、讲授流程管理课程。
|
目錄:
|
目 录
丛书序
前言
第1章什么是精益?
第1节精益管理的本质
【案例1】精益管理的产生
【理念1】现状绝不是最好的
【案例2】丰田公司的精益探索
【理念2】消除浪费,创造顾客价值
【案例3】精益,从日本到美国
【理念3】不断改善的精神
第2节精细化管理与精益管理
【案例1】细微之处可以积聚庞大的力量
【理念1】精细化管理
【案例2】将事情做到最好
【理念2】精益管理与精细化管理的区别与联系
第2章为什么要精益?
第1节价值创造
【案例1】本田汽车的价值追求
【理念1】企业的立足之本
【案例2】福特汽车的没落
【理念2】从客户需求出发
第2节浪费
【案例1】无处不在的浪费
【理念1】从系统的角度看价值创造
【案例2】某制造企业的精益改进
【理念2】用精益消除浪费
第3节精益管理在基层
【案例1】走动管理
【理念1】基层管理者的任务
【案例2】大野耐一圈
【理念2】从现场发现精益
第3章精益怎么做?
第1节“一个流”生产
【案例1】可乐罐的批量生产与等待
【理念1】批量生产和批量处理的误区
【案例2】没有价值的过程
【理念2】价值流认识与分析
【案例3】“一个流”改善
【理念3】建设快速、小批量的生产单元
第2节拉动式生产
【案例1】保险杠的拉式生产
【理念1】堆积的浪费
【案例2】丰田的看板制度
【理念2】拉动思维下的看板管理
第3节均衡化生产
【案例1】丰田公司按生产节拍供应物料
【理念1】节拍的均衡控制
【案例2】川崎造船的精益生产管理
【理念2】生产负荷的均衡化
第4章精益应该注意什么?
第1节效率的极限化
【案例1】伊藤洋华堂聚焦配送效率
【理念1】精益管理的效率要求
【案例2】丰田的标准化作业
【理念2】标准化助力效率提升
【案例3】僵化的标准
【理念3】关注标准化实施中的问题
第2节品质的保证
【案例1】丰田的质量门
【理念1】永远不要忽视质量
【案例2】石屋制果的逆境大反转
【理念2】正视品质问题
【案例3】日立电器的精益质量控制
【理念3】发现问题的自?P化技术
第3节成本的控制
【案例1】铃木汽车矢志于成本控制
【理念1】精益管理中的成本要求
【案例2】丰田的成本控制导致的质量危机
【理念2】降低成本不一定等于精益
【案例3】成本削减以质量为前提
【理念3】更全面的成本控制
第4节创新与变革
【案例1】SEVEN银行敢于抛开金融常识
【理念1】变革与价值创造
【案例2】三一集团的技术创新
【理念2】自主创造与借鉴
【案例3】丰田的“保守”心态
【理念3】技术应该起到协助作用
第5章如何自发做精益?
第1节人员推动精益
【案例1】不可或缺的精益人才
【理念1】精益的深层动力
【案例2】争取员工的信任
【理念2】全员精益的思维导向
第2节价值推动管理
【案例1】松下电器的“全员经营”
【理念1】上下同欲者胜
【案例2】丰田:共识下的决策
【理念2】争取最多的支持
【案例3】丰田的职业导师
【理念3】培养拥护公司理念的团队
第6章如何维持精益?
第1节循序渐进的精益
【案例1】精益,改善是没有尽头的
【理念1】精益永无止境
【案例2】大久保恒夫的高瞻远瞩
【理念2】精益无捷径
【案例3】花王日化30年利润增长的背后
【理念3】从小做起,多角度寻求精益
第2节循环改善
【案例1】丰田的循环改善
【理念1】建立循环改善系统
【案例2】找到问题根源
【理念2】彻底解决问题
【案例3】丰田的5WHY分析法
【理念3】深入探索问题原因
第3节让精益成为习惯
【案例1】3U备忘录
【理念1】养成随时记录问题的习惯
【案例2】日本电装的TPM落实
【理念2】全员参与到设备维护中
参考文献:
附录:
|
內容試閱:
|
精益管理leanManagement是管理学史上重要的一种管理思想。当今的很多企业,美国、日本尤其重视精益管理——而且不仅仅是生产制造业,第三产业、服务业也在运用精益管理思想。中国企业正在经历转型升级期,据我们的观察,在经历了2008年的经济危机之后,国内企业对精益管理的重视正在呈现直线上升的趋势,这恰恰是由精益管理的价值决定的——这一点我们后面会有深入的说明。
问题是,推行精益管理必须要有了解、运用精益管理思想和方法的人才队伍。所以,企业中的每一个基层管理者应当从了解、运用精益管理思想和方法的角度,学习精益,并将之运用于自己的管理工作中。
谈到精益思想,我们要关注的第一个问题:精益是什么。一直以来,对精益管理有各种各样的理解,但精益管理思想自始至终都存在三个基本理念:
(1)突破现状;
(2)消除浪费,创造顾客价值;
(3)发现问题并寻求改善。
【案例1】精益管理的产生
精益管理从它开始产生的那一天起,就是从对现状的突破开始的。
1950年,在丰田汽车任职的丰田英二到美国工厂进行了为期12周的考察,原本以为自己会对美国工厂制造流程与方法的进步大感惊叹,但是事实却不然。
他惊讶地发现,自1930年到当时这20多年间,大量生产方式竟然没有太大改变,即便这个生产制度本身存在着很多缺点。许多生产设备制造了大量半成品堆放储存,需要等待一段时间才会被送到另一个部门,以更大的设备制程处理该半成品,然后又堆放一段时间,再送到下一个制程。
这样的生产方式造成了很多问题:这些步骤之间的中断导致大量材料成为等待输送的存货;所谓“降低每单位平均成本的效率”不过是使设备和员工不停地生产,而这种大量生产同时又造成产出过剩和产品瑕疵等问题;到处可见的大型起货机卡车在搬运大批原料,工作场所缺乏组织与管控,工厂看起来更像是仓库……
这些问题被丰田英二看在眼中,但他没有时间表达感慨,因为,他看到了丰田超越的机会。丰田英二在他的考察报告中写道:“那里的生产体制还有改进的可能”,并指派大野耐一:“迎头赶上福特汽车公司生产力”。
这项工作恰好符合大野耐一内心中涌动着的偏执狂精神,他开始深入地研究一种新兴的生产方式。精益生产正在悄悄地孕育。
【理念1】现状绝不是最好的
精益思想的产生有它的背景。
20世纪初,美国福特汽车公司创立了世界上第一条汽车生产流水线,它通过标准化、大批量的规模化生产方式迅速降低了生产成本,提高了生产效率,一举将汽车这种曾经属于少数富人的奢侈品变成了大众化的交通工具。自此,大规模的生产流水线始终被人们视为现代工业生产的主要特征。但是,自第二次世界大战以后,整个社会进入了市场需求多样化的新阶段,工业生产也随之向多品种、小批量的方向发展,单品种、大批量的流水线生产方式的弱点日趋明显。
这些弱点就集中体现在:
(1)大批量的制造同质产品难以销售出去,造成大量的产品过剩。
(2)客户需要小批量采购时,大批量生产无法适应客户的需求。
今天很多企业面临的经营环境也是这样的困境:消费者的需求不仅多样化,更新的速度也越来越快。我们今天很多生产加工企业当然更需要朝向多品种、小批量的柔性生产方向发展,这是企业竞争力的源泉所在。但是,在当时只有丰田公司看到了其中的机遇,开始寻求适应时代发展的新型生产方式,这才推动了精益生产的诞生。
关键在于,精益管理从一开始就是寻找突破,这是精益管理思想中最核心的理念之一。这一理念也意味着,现状绝不是最好的,管理者也好,员工也罢,都绝不能仅仅满足于现状。
【辅助阅读】洛克菲勒与“38滴型”焊接器
世界第一个亿万富翁、被称为“石油大王”的约翰?洛克菲勒,年轻时在一家石油公司工作。初入石油公司,由于既没有学历又没有技术,洛克菲勒便被分配去检查石油罐盖有没有自动焊接好。这是整个公司最简单、枯燥的工序,公司里的人都说这是三岁小孩都能做好的工作。
洛克菲勒的主要工作就是:看着焊接剂自动滴下,然后沿着罐盖转一圈,再看着焊接好的罐盖被传送带移走。洛克菲勒对自己的工作非常负责,他从不曾偷懒耍滑。每一次,他都会认真观察罐盖的焊接质量。时间久了,他发现每当焊接器都要滴落39滴焊接剂之后,一个罐盖的焊接工作就完成了。然而,在计算过他观察到的每滴焊接剂的滴量之后,他发现只要38滴焊接剂就可以将罐盖完全焊接好。
经过多次观察,他确定自己计算的结果是正确的。因此,他开始着手研究只滴38滴焊接剂的焊接器。经过反复测试、实验,“38滴型”焊接器最终成型。使用这种焊接器焊接的石油罐盖,质量和原来的一样,但是却可以比原先节约了一滴焊接剂。就是这一滴焊接剂,一年就可以为公司节约出5万美元的开支。
我们的工作中
|
|